Fast construction methods and flexible processes benefited this large-scale apartment complex on Auckland’s North Shore.
A unified architectural treatment and materials palette can be seen throughout this 5,800 sqm trio of apartment buildings on a ridgeline in Birkenhead. Overlooking the Hauraki Gulf, Rangitoto and Auckland’s CBD, the high-profile development features a variety of cladding styles including vertical standing seam roofing, precast panels and composite aluminium cladding by Symonite.
‘Each system has its own installation techniques,’ says Sam Michelsen, project manager at Waide Construction, ‘and Symonite brought the detailing and fabrications skills needed to interface with the structure and other cladding trades, discussing solutions with the architect, so they could come to site and install their products in the most efficient and professional way.’
Site measuring and prefabrication to speed up installation
Symonite coordinated closely with the builder during pre-construction meetings, so the builder knew exactly what was required by the façade team for ultimate efficiency. Windows, flashings and downpipes were all installed and the flooring was down, so Symonite could site measure and check all tolerances before fabrication. This attention to detail meant that once the aluminium panels arrived on site, they fitted into place neatly and accurately.
‘We aligned all our panel joints and set the tolerances to speed up the installation,’ explains Symonite’s project manager Ranesh Prasad. ‘Depending on the project, fabrication typically takes three days and installation of the panels usually takes two days. We can have three to four installation teams at any one time on a project of this scale, all working ahead of the fabrication teams for optimum productivity and efficiency.’
Resequencing the programme to work around procurement delays
One of the architectural features is a large area of angled aluminium façade just below the penthouse apartments. Rather than a traditional timber sub-structure, Symonite developed customised metal brackets to create the taper. ‘These are made in our factory and sequenced in the right order for the team on site,’ says Prasad. ‘Instead of the chippies needing to build the substructure, our team could prefabricate the brackets to achieve the desired architectural forms and speed up the installation period for the main contractor.’
During one phase in the project, the programme needed re-sequencing due to procurement issues beyond the construction team’s control. ‘In a typical sequence, the facade is built first and the construction works its way inwards to the interior fit-out,’ explains Michelsen. ‘In this case, we had to build the interior behind the exterior cladding – working between the two elements.’
Going the extra mile
‘Symonite are a one-stop shop, offering practical design and programming advice, and coming up with options, alternatives and innovations,’ Michelsen says. ‘They provided a flashing service that was not originally in their scope and increased resources on site as required. At one stage, they had 30 guys on site and some of them worked through the Christmas periods and public holidays. Overall, they went the extra mile and were a real asset to the project.’
—
CREDITS
Project: Chelsea Bay Apartments
Product: Reynodual
Facade Engineer: Loutrec Facade Design
Main Contractor: Waide Construction
Completed: 2020
Photographer: Intense Photography
Writer: Folio
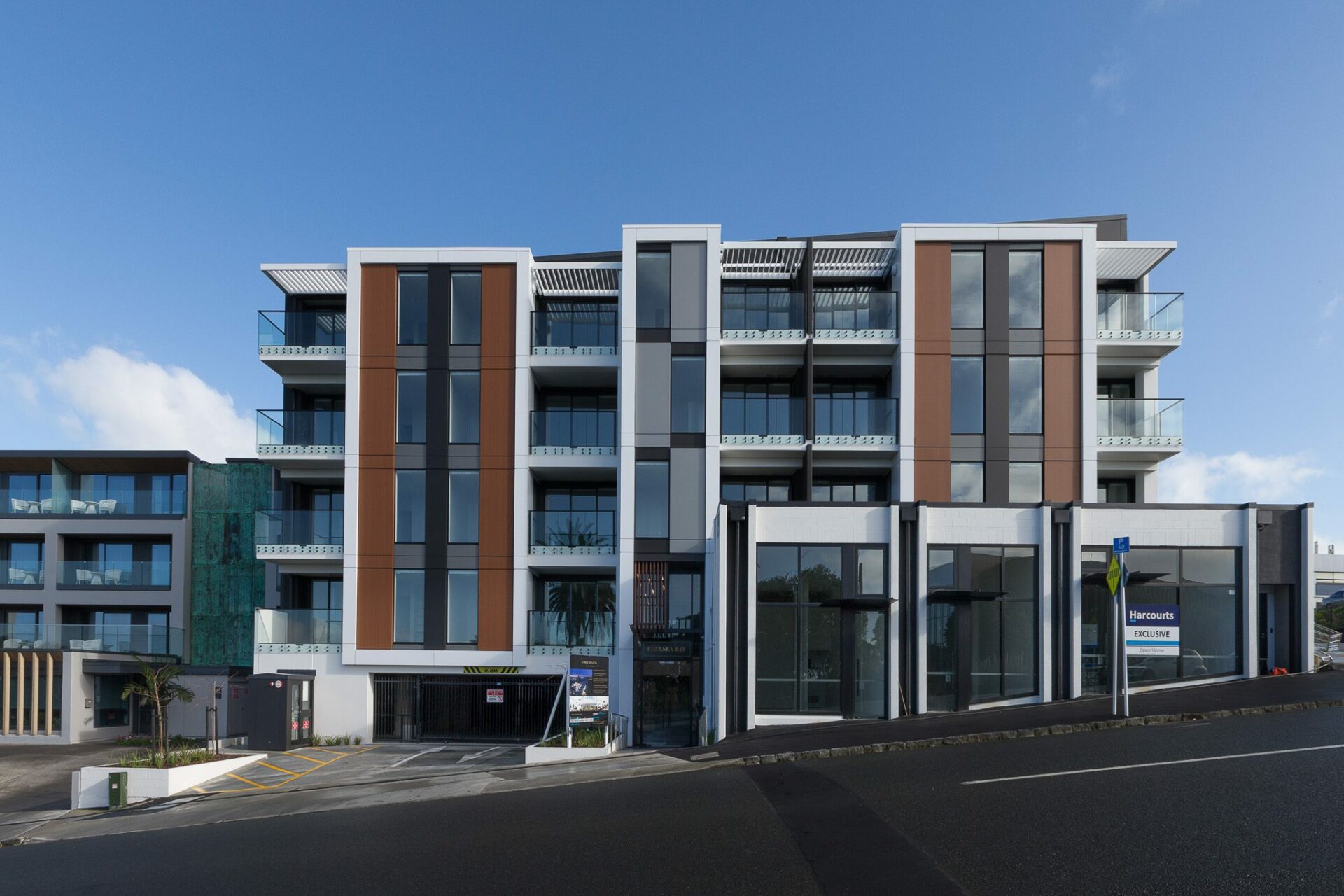
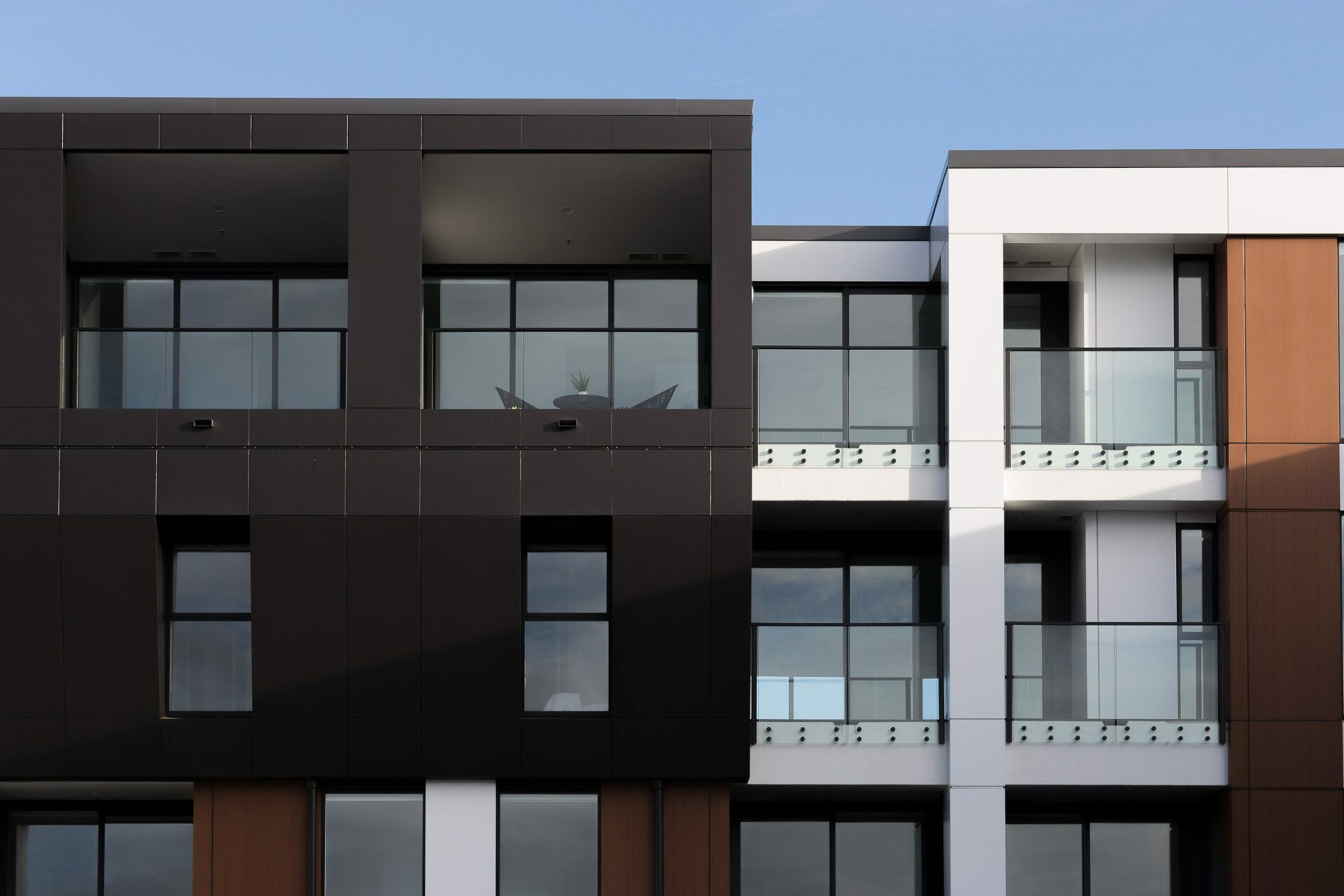
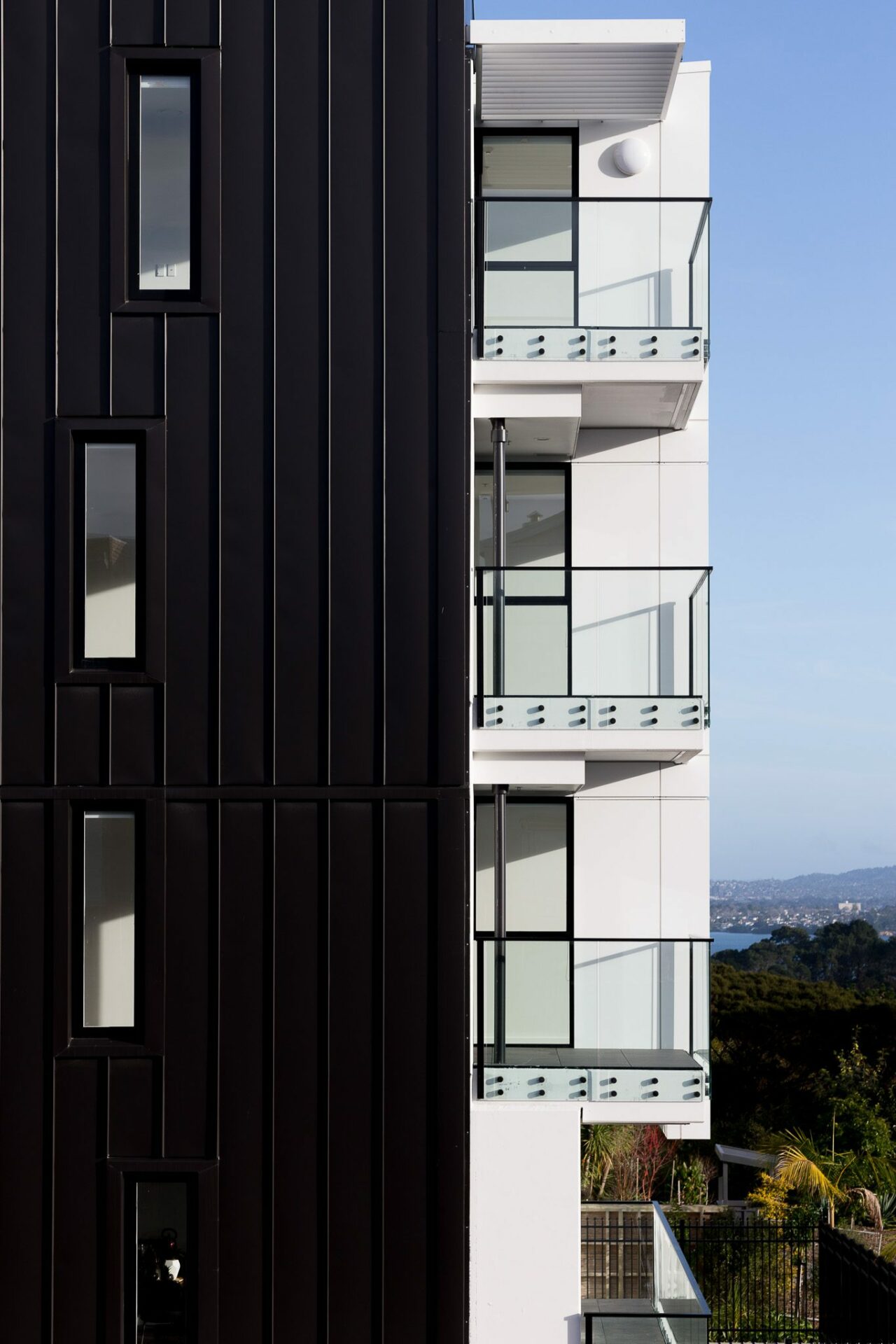
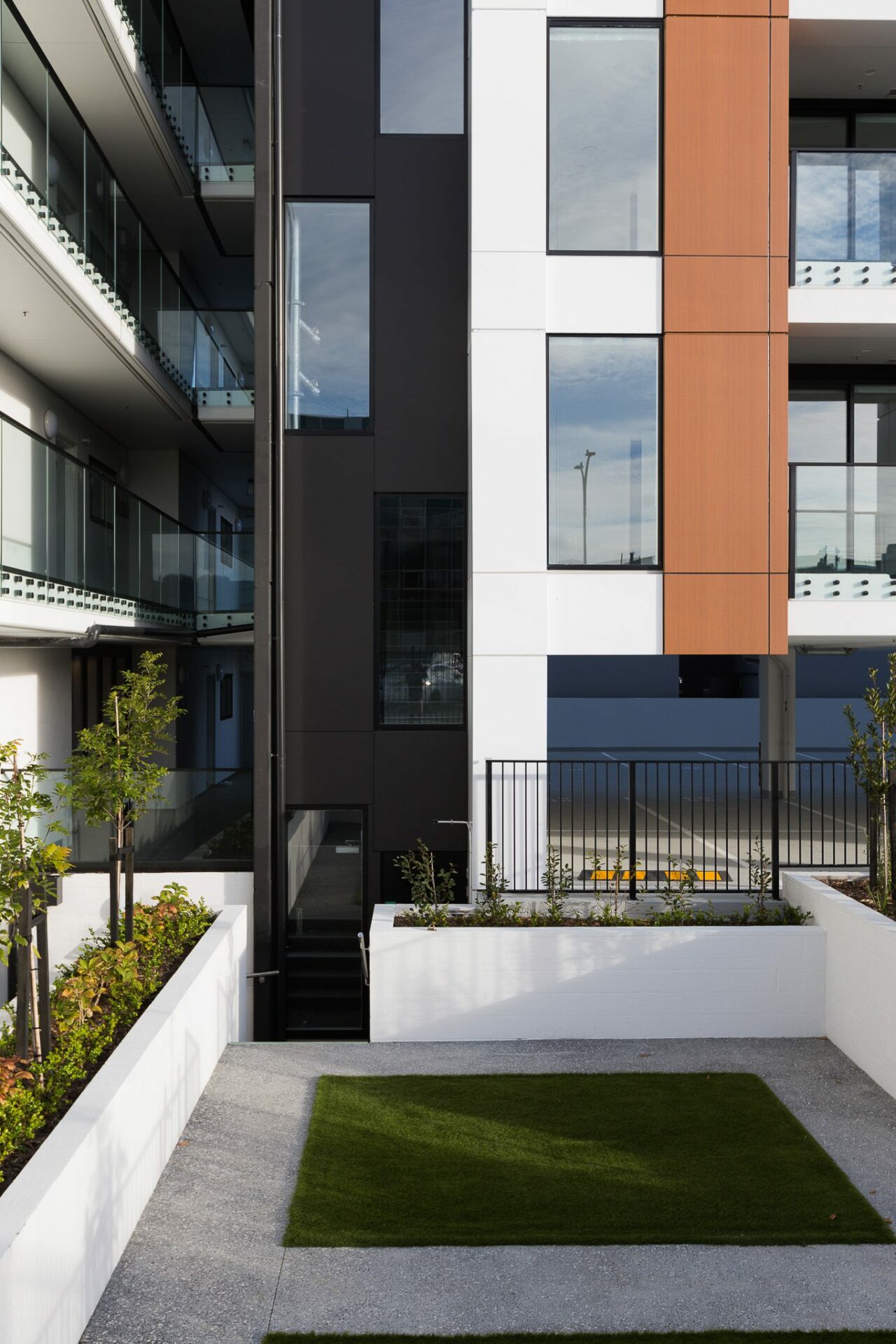
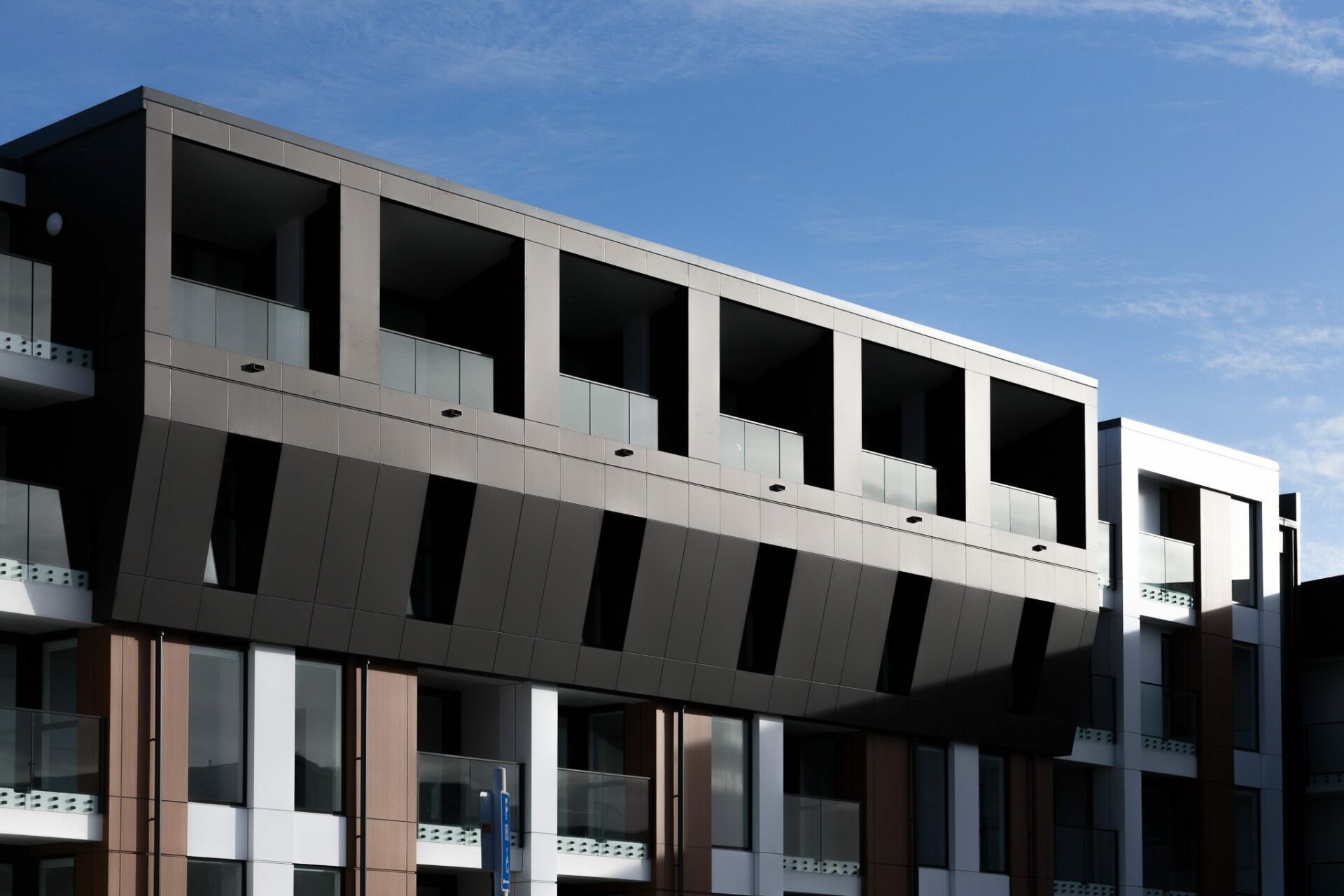
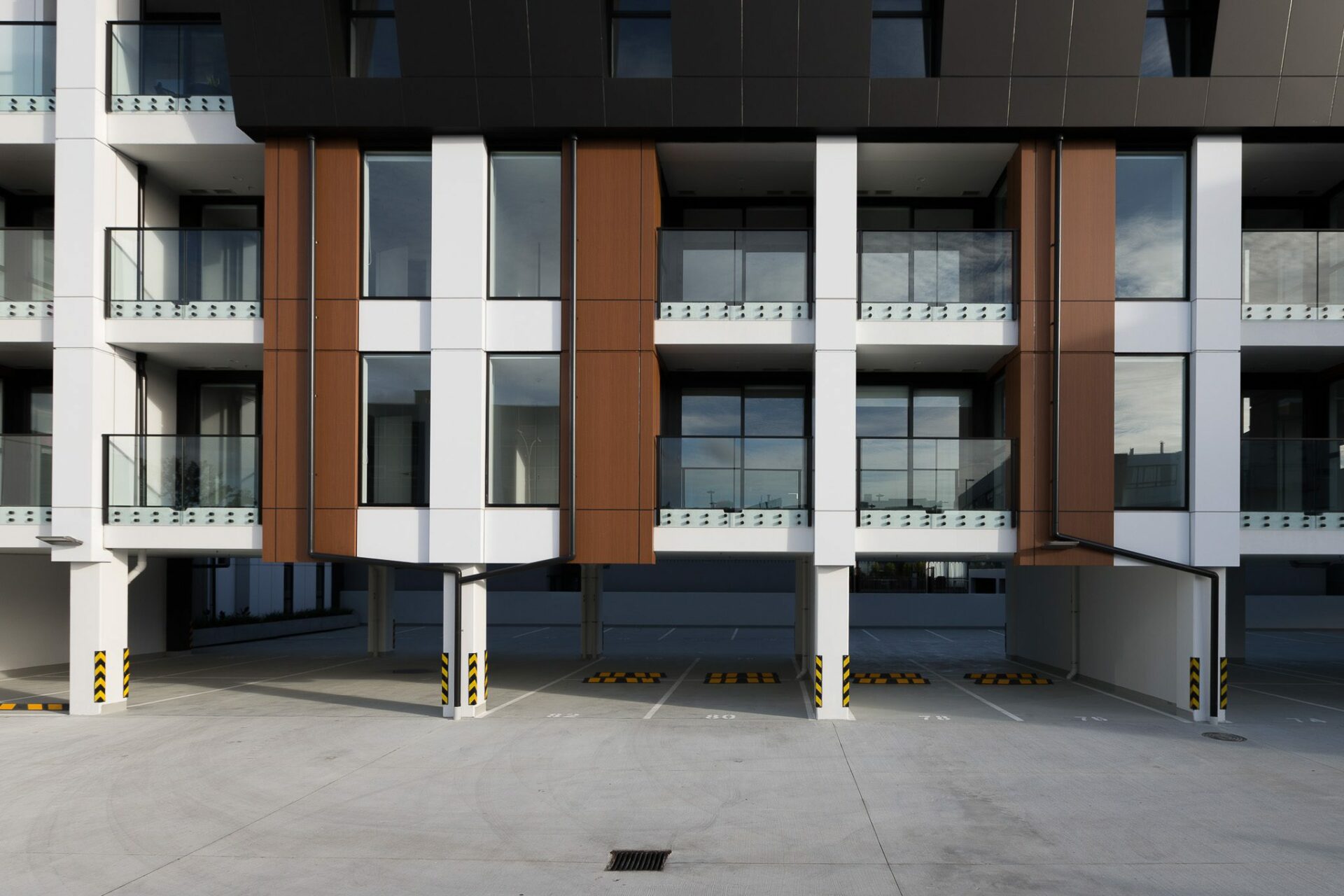