Photo: c/- NZ Strong
The first of the new generation of Metlifecare retirement villages represents the changing face of retirement communities, offering resort-style living through to hospital-level care for its residents.
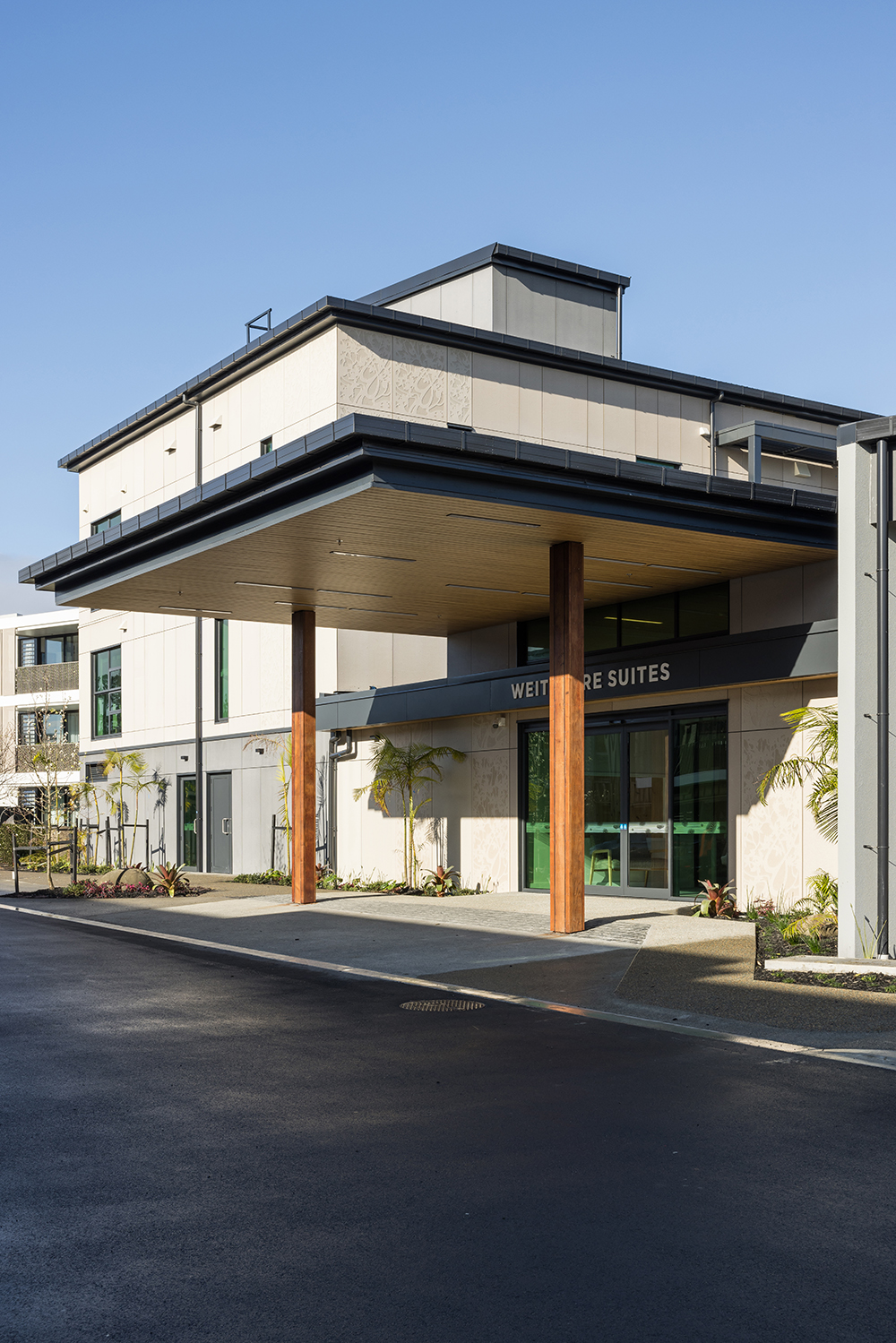
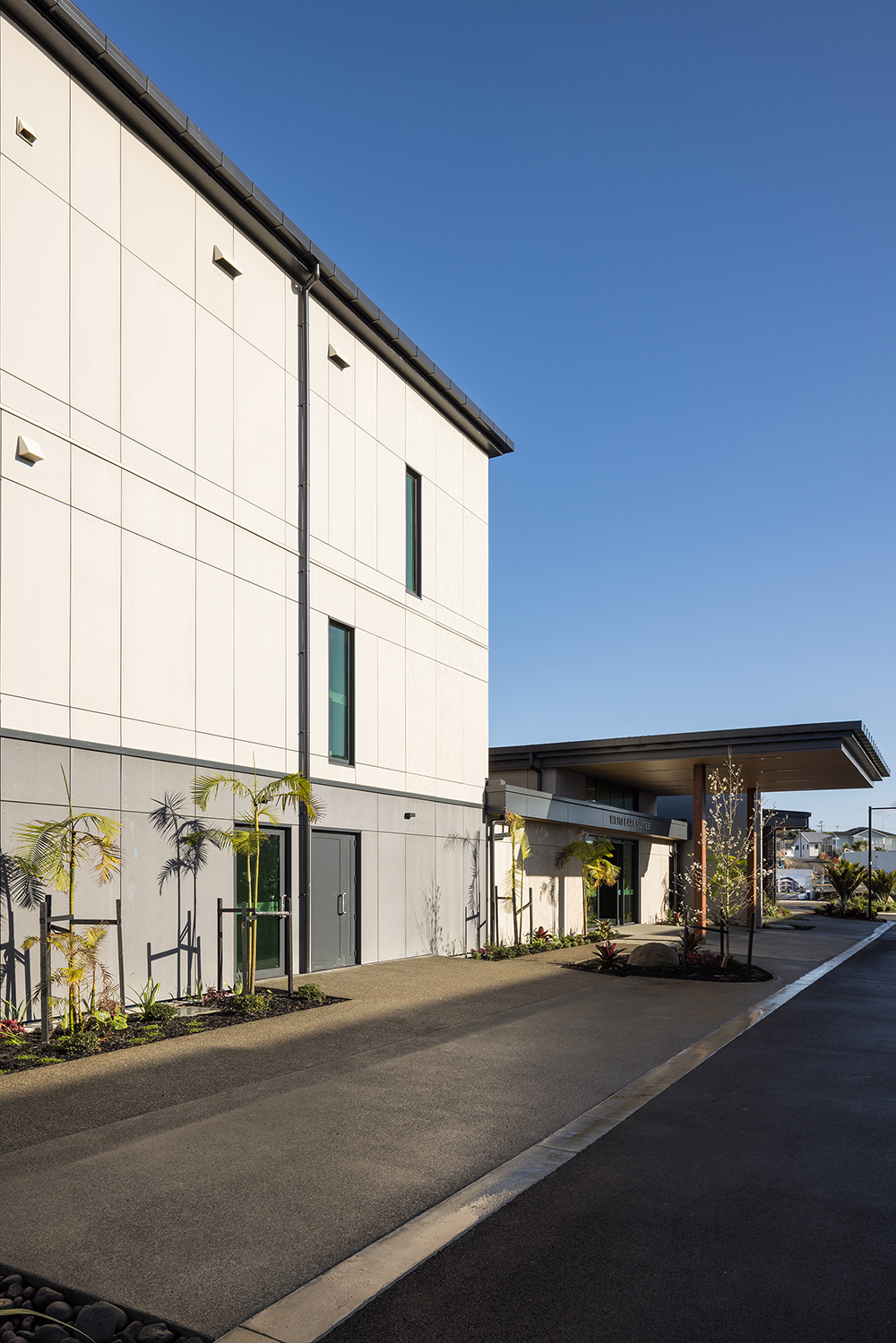
From the beginning, Metlifecare’s bold vision for Gulf Rise at Red Beach required a new approach to design and construction. Symonite’s Full Façade service provided a modular internal/external wall assembly based on mass timber construction that would speed up and simplify façade construction for main contractor NZ Strong Construction.
‘We were a big part of the journey,’ says Symonite’s Project Director Houssein Daakour. ‘Metlifecare wanted a true modular system, so we worked closely with the Metlifecare in-house team, NZ Strong and Ignite Architects to develop prefabricated units that could be completed in our factory and then easily installed on-site.’
Pre-construction modelling for better design
‘The project went through two stages of early coordination – the building consent stage, and then the second stage of services coordination post-consent,’ says Matthew Harris, Symonite’s Senior Technical Advisor. ‘For these, we completed preliminary design in principle drawings, shop drawings and engineering calculations in-house, supervised by our façade engineer.’ The scope included lightweight steel stud, Weatherline, Pro Clima, external insulation, high-density through-colour fibre cement, windows and doors. These components were installed off-site within modular panels, and then transported to the site.
Preconstruction modelling was done using AutoCAD software. These were then coordinated with Ignite’s BIM model and issued under the Revisto platform. ‘That’s when we get into the nuts and bolts of the services that are defined in full post-consent and need to be coordinated and clash detections checked for the off-site modular build,’ says Matthew.
Primary considerations driving the modular design were thermal comfort, speed of construction, durability, product selections, and design aesthetics. The end result was a series of pre-fabricated panels complete with structure, studs, flashings, cladding, and thermally broken windows, which arrived on-site finished, numbered and ready to be craned in.
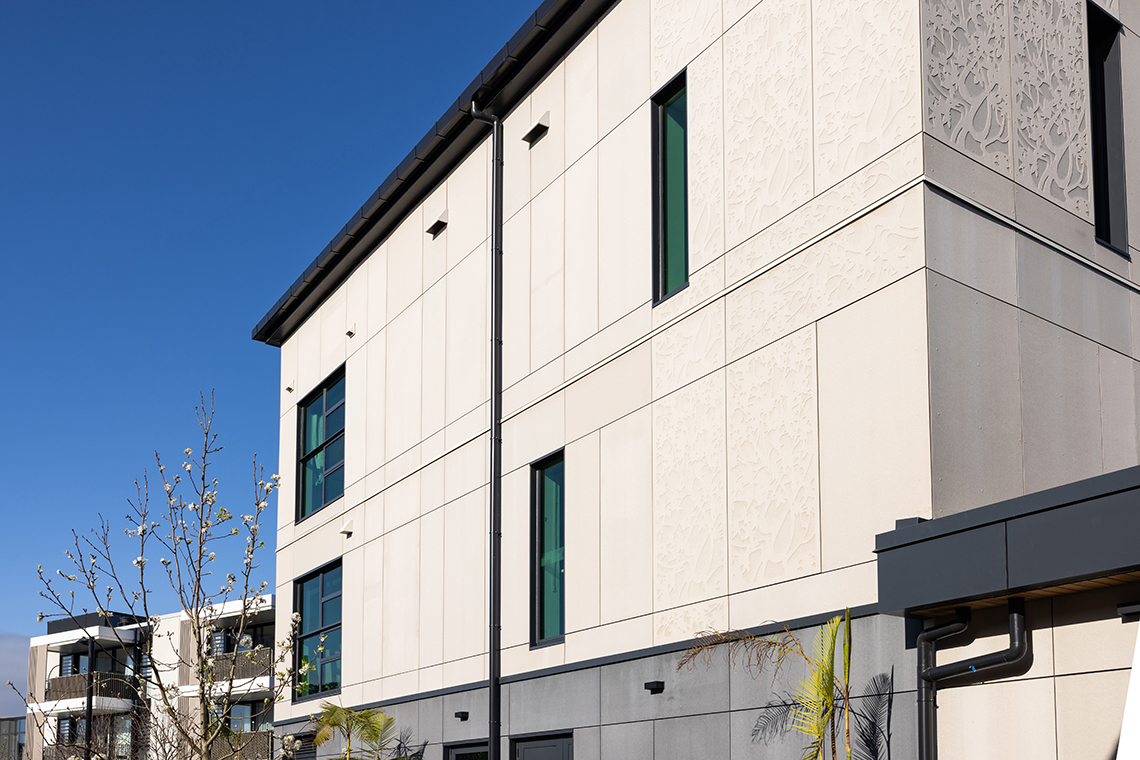
A new way of combining walls and superstructure
The head for the panels is a glulam beam, which forms a part of the superstructure. ‘The staging crew sent us the beams and we hung our walls from them,’ says Matthew. ‘Part of the challenge was developing waterproofing details in bringing these panels together – the weather-proofing zip between modular panels.’
‘With the glulam beams part of the structure, we became an integral part of the sequencing on site. The mass timber walls were stood up, then braced, then our modular panels were lifted by crane into location and the walls were bolted together at each end.’
This was one of Symonite’s key innovations – taking parts of the superstructure off-site, adding the external walls and fixtures before lifting and installing them on-site. Working completely in the BIM environment allowed the process to proceed directly from digital design to fabrication in factory conditions, with much finer control and accuracy.
Reducing the number of trades on-site
Another advantage of the modular system was the substantial reduction in the number of people working on-site. ‘Six different trades were working in the factory, but only one for the installation,’ says Houssein. ‘Fewer people accessing the site and using the surrounding roads made for a better Health & Safety result.’
‘And because all the panels were craned in, there was no need for an external scaffold for installation. We used scissor platforms, cherry pickers and just a small amount of scaffolding for the final fix of the external flashings.’
—
PROJECT CREDITS
Designer / Architect: Ignite Architects
Builder: NZ Strong Construction
Photographer: Mark Scowen
Writer: Folio
Find out more
To learn more about our Symonite’s Full Façade service, get in touch with our team of experts.
Other Symonite FULL FACADE projects…